Industrial Centrifuge Systems
- Home
- »
- Products
- »
- Water & Wastewater Treatment Solution
- »
- Centrifuge Systems
Solids-water separation using centrifugal force!
Industrial centrifuge systems are excellent industrial wastewater treatement solutions for streams that are high in suspended solids. In a centrifuge, the solids are separated from the liquid phase using a centrifugal force of up to 2,417 G. This results in a clean water stream that can either be discharged to the POTW or reused in your process.
Basket Style Centrifuge Systems
Basket style centrifuge systems are characterized by their rugged, easy-to-operate design. The following is a typical process overview.
-
Feed: Wastewater is pumped or gravity fed from an up-stream holding tank to the integral feed tank located on the centrifuge system skid. Optional separation enhancement chemistries are dosed into the feed tank and mixed into the waste stream at this time.
-
Separation: Wastewater is pumped from the feed tank into the centrifuge basket which is spinning at extremely high speeds to generate a strong centrifugal force. As a result, the higher density solids move to the outside of the bowl while the lower density clean water exits the bowl into the clean water tank.
-
Cleaning: Clean water is pumped to the on-skid clean water receiver and eventually pumped to a clean water holding tank while the waste solids are left behind inside the bowl. Once the bowl is filled with solids, the system will notify the operator that the bowl needs to be removed and emptied before restarting the system.
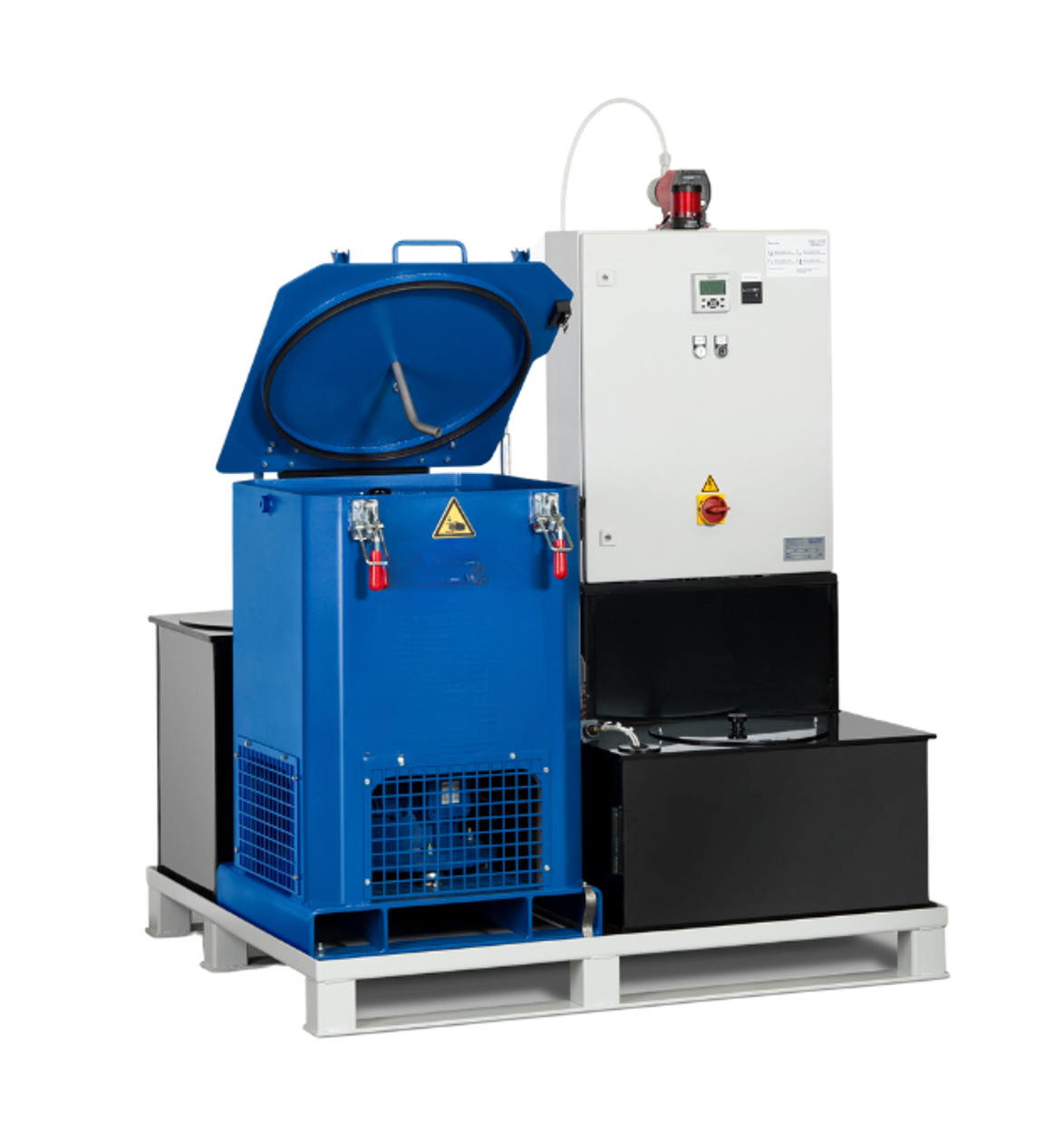
Automatic Peeling Centrifuge Systems
Automatic peeling style centrifuge systems have a similar sequence of operation as the basket style centrifuge, except instead of manually removing solids, the sludge deposited in rotary drum is automatically peeled out and dumped into a sludge holding container.
The automatic peeling systems are engineered to maximize throughput while significantly reducing the need for manual cleaning interventions. These advanced centrifugal sludge dewatering systems are capable of processing up to 530 gallons per hour, ensuring high efficiency and consistent performance. By automating the peeling process, you not only streamline operations but also enhance overall productivity, making it an ideal solution for high-capacity processing environments.
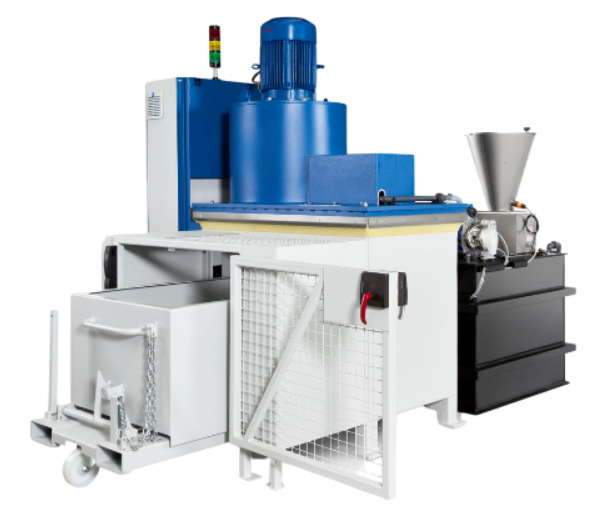
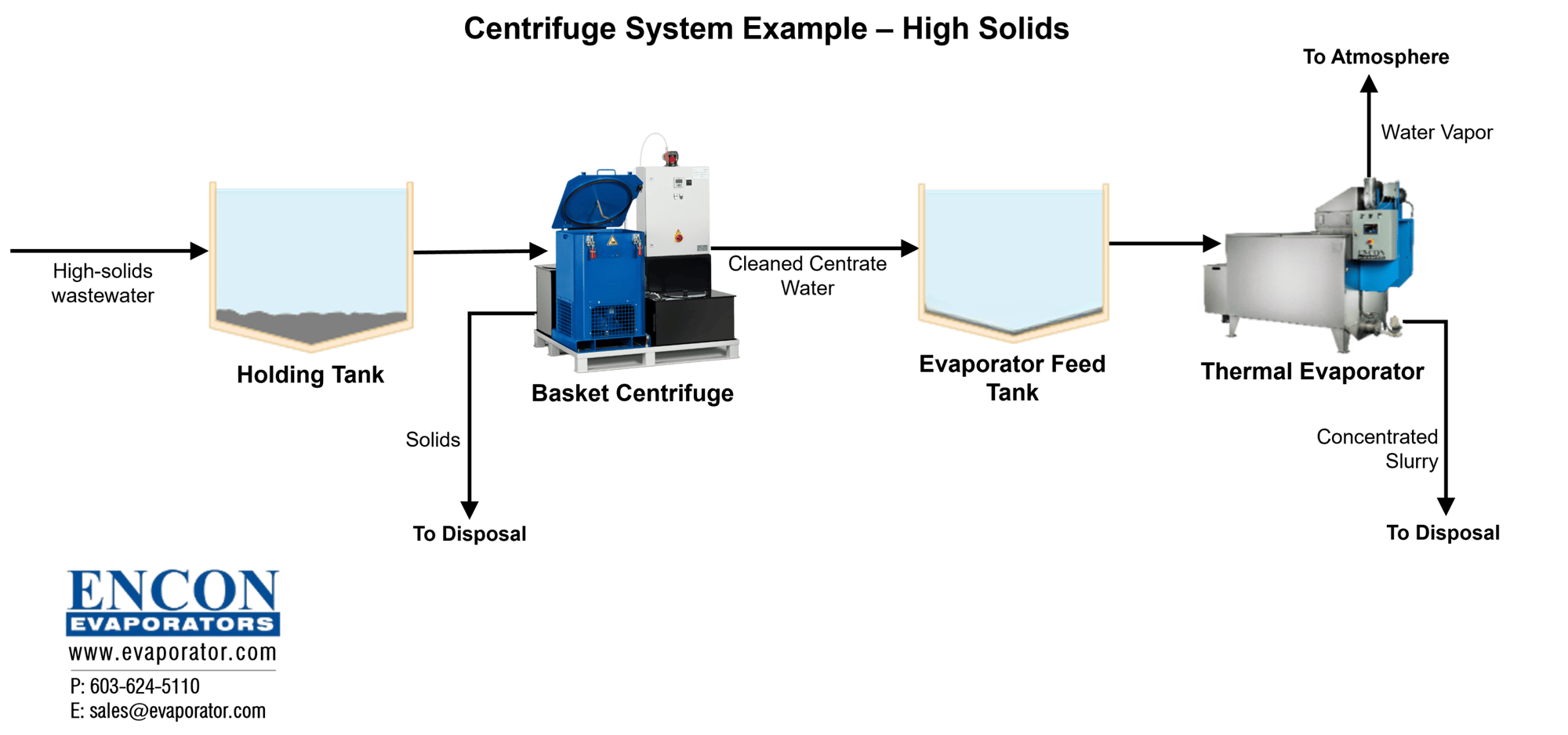
Typical Industrial Wastewater Applications for Centrifuge Systems:
- Industrial/Commercial Painting: paint booth cleaning wastewater
- Corrugated Paper Product Manufacturing: inks, dyes, and adhesives
- Surface Finishing: vibratory finishing wastewater and other wastewater entrained with metals, ceramics, and other media
- Food & Beverage: vegetable oil, animal fats, brine solutions
- Shipping & Maritime: oily bilge water
- Heavy Equipment: oily wash water from cleaning parts
- Chemical Manufacturing: plant CIP wastewater entrained with oils
- General Industrial: oily wastewater entrained with contaminants such as solids
Full Range of Upgrades, Accessories and Services to Unlock Your Evaporator’s Full Potential
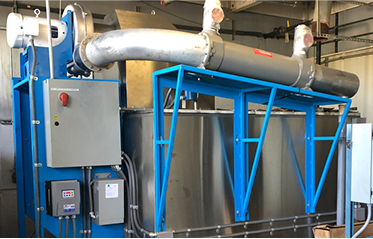
ENCON offers a full range of upgrades, accessories and services to minimize labor and maximize return on investment.
Recover your wastewater as clean condensate with our condenser package!
Work with our consultative Sales Engineers to spec a turn-key system.
Utilize our air permitting / permit-exemption services.
Automate with auto-dump or auto-oil-decant.
Free Application Feasibility Report
The centerpiece of our consultative approach is our complimentary bench scale analysis of your waste or process stream. This free analysis determines:
- How appropriate the stream is for evaporation
- Estimated reduction percentage
- Recommended materials of construction
- Recommended operating procedures.
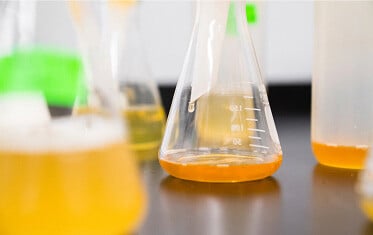
Why Choose ENCON?
Superior Service & Support – We provide industry-leading technical support, ensuring customers receive prompt and knowledgeable assistance.
Consultative Sales Approach – Our expert sales engineers guide you through the process, including a detailed boil analysis of your waste stream to tailor the perfect evaporator solution.
Proven Industry Experience – With over 2,000 installations worldwide, ENCON evaporators are trusted by some of the largest companies, including 3M, GM, Ford, and Caterpillar, for their reliability and performance.
Wide Range of Heat Source Options – The most extensive selection of heat sources in the industry, ensuring the most cost-effective solution for any application.
Largest Thermal Evaporators in the Market – Designed to handle the most demanding industrial needs, with larger capacities than competitors. Proudly designed and manufactured in the USA.
Unmatched Reliability & Performance – ENCON evaporators are built for longevity, offering superior technical advantages and reliability over competitors.